Injection molding is one of the most widely used manufacturing processes, essential for creating a vast array of plastic parts including our favorite toys like LEGO sets. Known for its efficiency, versatility, and scalability, injection molding is pivotal in industries from automotive to consumer electronics. Here’s everything you need to know about injection molding, from the basics of how it works to its benefits and challenges — look no further.
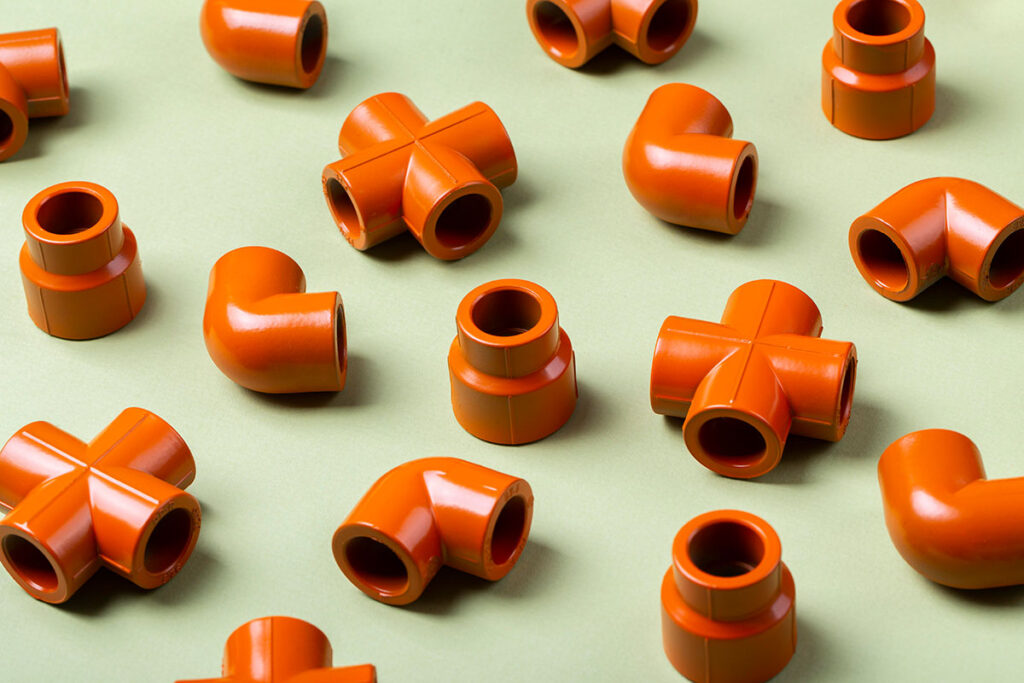
Understanding the Injection Molding Process
Injection molding involves melting plastic material and injecting it into a precisely shaped mold cavity. This process begins with feeding plastic granules into a hopper, where they are heated until they reach a molten state. Then, using a high-pressure plunger, the molten plastic is forced into a mold cavity, which cools and solidifies into the desired shape.
The cycle time for each part is relatively short, making injection molding ideal for large-scale production. Depending on the complexity of the design and type of plastic used, cycle times can vary but often last only seconds. For high-quality results, work with an experienced provider. You can go here and look into professionals who offer plastic injection molding services to ensure consistent quality and efficiency in production. Once the part solidifies, the mold opens, and the component is ejected, ready for further processing or assembly.
Types of Materials Used in Injection Molding
The choice of material determines the part’s durability, flexibility, and appearance. Thermoplastics are the most commonly used materials because they can be melted, reshaped, and reused without losing their properties. Some popular thermoplastics include polypropylene, polyethylene, and polystyrene.
Thermosetting plastics and elastomers are used when specific properties are required. Thermosetting plastics harden permanently after being molded is perfect for heat-resistant components. Elastomers, on the other hand, add flexibility to products like rubber seals. The selection of the right material depends on its intended use, mechanical properties, and cost.
Benefits of Injection Molding for Manufacturing
Injection molding offers several advantages, particularly in terms of efficiency and consistency. The process allows for high production rates, with machines capable of producing thousands of identical parts in a single run. This high-speed production makes injection molding cost-effective for large orders where each part’s cost drops as volume increases.
Another benefit is the high degree of design flexibility injection molding provides. Complex shapes, intricate details, and multiple components can be all created in a single mold, eliminating the need for extensive assembly. Automation is common in injection molding facilities, reducing the chances of human error and improving overall quality. Companies in industries requiring large volumes of precise components often turn to injection molding for these reasons as it balances speed and quality effectively.
Common Challenges and Limitations of Injection Molding
While injection molding comes with a huge set of benefits, it does have its challenges and limitations. One of the most significant ones is the high upfront cost of mold creation. Molds are made from hardened steel or aluminum, requiring precise machining to ensure they meet exact specifications.
Design modifications might be a bit complex to apply — once a mold is created, altering it can be costly and time-consuming. Shrinkage, warping, and material limitations can also pose challenges when working with complex shapes or specific material properties. Injection molding is best suited for high-volume production; smaller runs may not justify the initial setup costs. Addressing these challenges early in the planning stage can mitigate issues and ensure smoother production.
Applications of Injection Molding Across Industries
Thanks to its ability to produce consistent, high-quality parts, injection molding is integral in numerous industries. In the automotive sector, injection-molded components like dashboards, bumpers, and interior fixtures are standard. Consumer electronics also rely heavily on injection molding for creating housings, connectors, and internal parts.
Medical devices, which require high precision and biocompatibility, are another major application area. Injection molding allows manufacturers to produce safe, sterile, and reliable medical tools and components. Even household items, from kitchenware to storage containers, often result from injection molding. This process is the go-to solution for industries that prioritize volume, accuracy, and material consistency.
Environmental Impact and Sustainability in Injection Molding
As industries prioritize sustainability, injection molding has adapted to incorporate eco-friendly practices. Many manufacturers are adopting recycled plastics, reducing the need for virgin materials, and lowering overall environmental impact. Some facilities also implement closed-loop systems, where excess plastic from one production cycle is reused in another, minimizing waste.
With newer injection molding machines using electric rather than hydraulic power, you can easily reduce energy consumption. Advancements in mold design now allow for quicker cycle times and optimized material use, further decreasing resource usage. Biodegradable plastics and biocomposites are also gaining popularity in injection molding while providing sustainable options for industries aiming to reduce their carbon footprint. By embracing these sustainable practices, injection molding not only meets industry needs but also aligns with environmental goals.
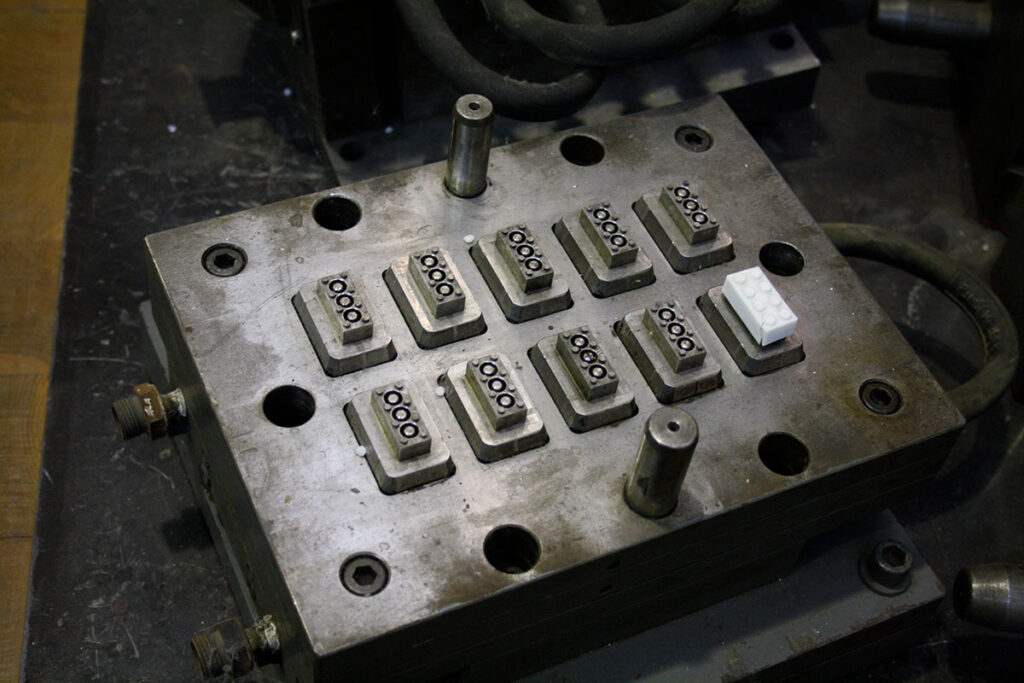
Once businesses across all sectors understand injection molding’s capabilities, they can better leverage the technology to meet their production goals. Whether for small consumer products or complex automotive parts, injection molding delivers high-quality results at scale.