Quality control is essential for ensuring the safety and reliability of finished products. By implementing effective quality control procedures, manufacturers can catch and correct defects before they cause any harm. In this article, we will discuss different methods for inspecting finished products, including visual inspection, metal detection, x-ray inspection, and track and trace solutions. We will also define what needs to be inspected and how to create a procedure for handling defects. So, without further ado, let’s get started!
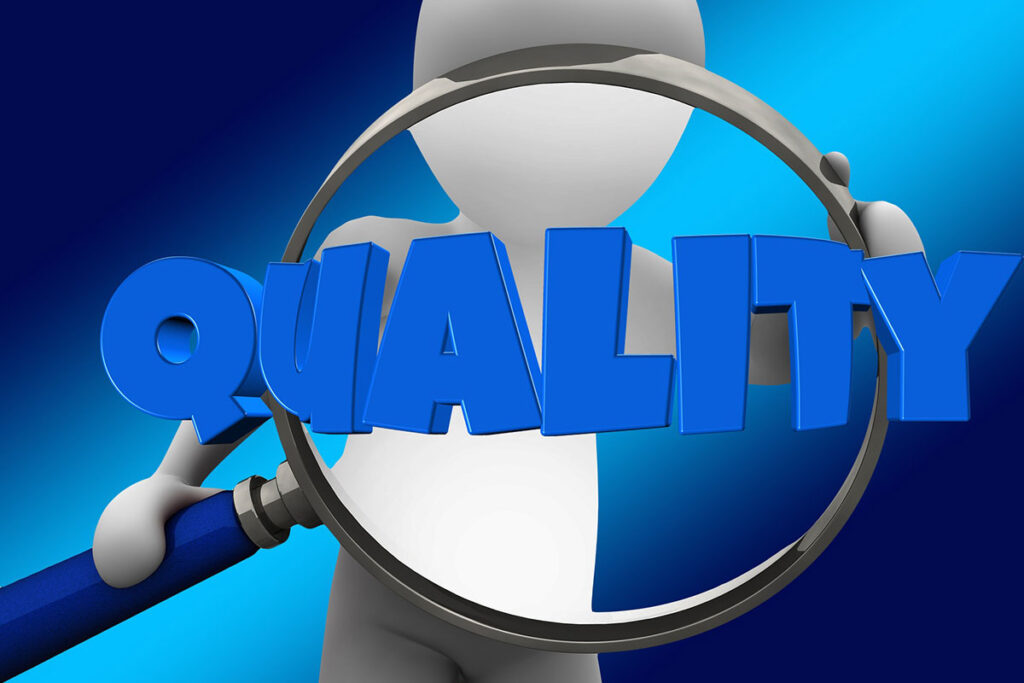
Visual Inspection
Visual inspection is one of the most common methods for quality control. It involves looking at products to check for defects. This can be done by hand or with the help of machines. You can even find remote visual inspection products that allow you to inspect products from a distance. There are many different types of visual inspection, but some of the most common are surface inspection, dimensional inspection, and assembly inspection.
Surface inspection is used to check for defects on the surface of products. This can be done with the naked eye or with the help of magnifying devices. Dimensional inspection is used to check whether products meet the required specifications. This includes checking dimensions such as length, width, and thickness. Assembly inspection is used to check whether products have been assembled correctly. This can be done by hand or with the help of machines.
Metal Detection
Metal detection is another common method for quality control. It involves using a machine to scan products for metal contaminants. This is important because metal contaminants can cause serious health problems if they are ingested. There are two types of metal detectors: handheld and inline. Handheld metal detectors are portable and can be used to scan products for metal contaminants, while inline metal detectors are installed in production lines and can automatically scan products for metal contaminants.
Performing metal detection procedures is especially important for food manufacturers, as metal contaminants can cause food poisoning.
X-Ray Inspection
X-ray inspection is a type of quality control that uses x-rays to check products for defects. This is important because it allows manufacturers to find hidden defects that could not be found with visual inspection or metal detection. X-ray inspection can be performed manually or automatically. Automatic x-ray inspection is often used in production lines, as it can scan products quickly and efficiently. X-rays can detect a variety of defects, such as cracks, voids, and foreign objects. In addition, x-ray inspection can also be used to check the quality of welds.
Track and Trace Solutions
Track and trace solutions are a type of quality control that uses RFID tags or barcodes to track products throughout the manufacturing process. This is important because it allows manufacturers to identify where defects occur so that they can be corrected. Track and trace solutions can also be used to track the movement of products through the supply chain. This is important for ensuring that products are delivered to the correct customers on time. Also, track and trace solutions can be used to monitor the shelf life of products.
Define What Needs To Be Inspected
Now that you know about some of the different methods for quality control, you need to define what needs to be inspected. This will depend on the product that you are manufacturing. For example, if you are manufacturing food products, you will need to inspect for contaminants such as metal contaminants or bacteria. If you are manufacturing electronic products, you will need to inspect for defects such as cracks or voids. Once you have defined what needs to be inspected, you can create a procedure for handling defects.
Create A Procedure For Handling Defects
Once you have identified the defects that need to be corrected, you need to create a procedure for handling them. This will involve creating a process for repairing or replacing defective products. In some cases, it may be necessary to scrap the entire batch of products. This is especially true for food manufacturers, as contaminated food products can cause serious health problems.
When creating a procedure for handling defects, you need to consider the following factors:
● The type of defect that has been found
● The severity of the defect
● The number of defects that have been found
● The cost of repairing or replacing the defective product
● The impact of the defect on the customer
After you have considered these factors, you can create a procedure for handling defects. This procedure will ensure that your products meet the required quality standards and that your customers are satisfied.
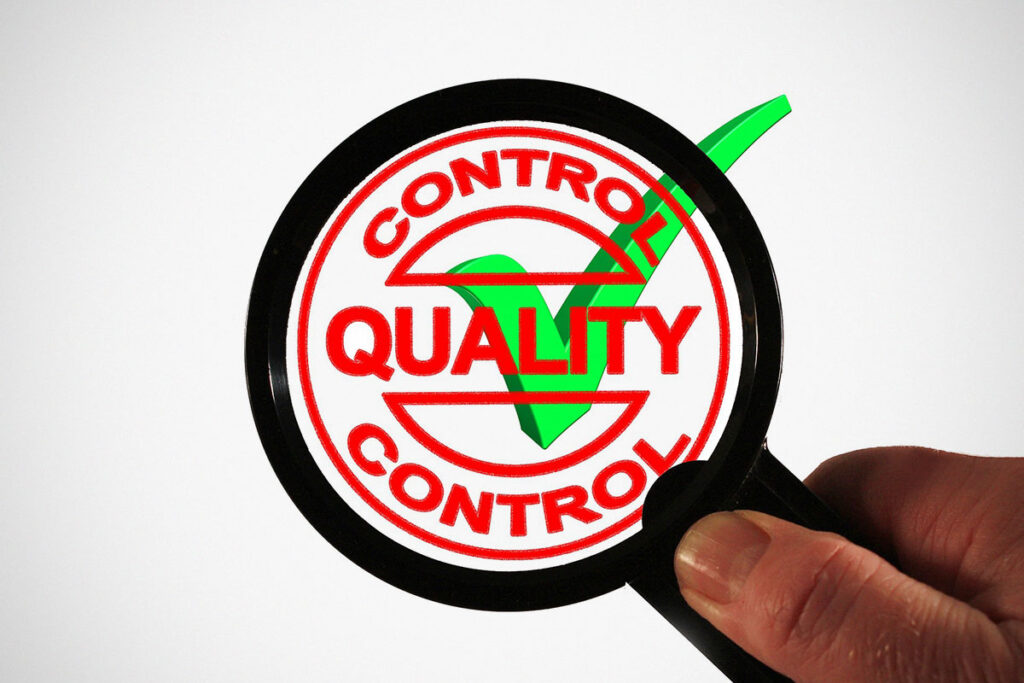
There are many different methods that can be used to ensure the quality of finished products. In this blog post, we have discussed some of the most common methods, including visual inspection, metal detection, x-ray inspection, and track and trace solutions. In addition, we’ve also discussed the importance of defining what needs to be inspected and creating a procedure for handling defects. By using these methods, you can ensure that your products meet the required quality standards and that your customers are satisfied.